The State of Shipping and Potential Supply-Chain Solutions to Refresh World Markets
- Jason Angle
- Nov 25, 2021
- 11 min read
Updated: May 11, 2023
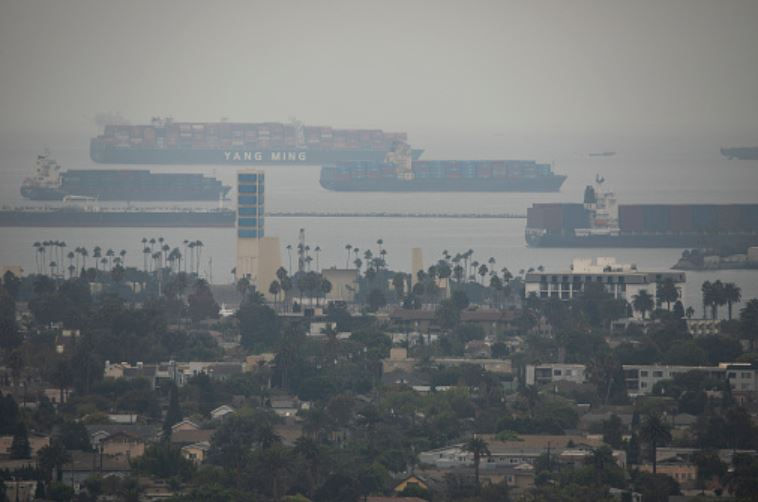
Intro: Why We're Looking for Supply-Chain Solutions
With 2021 coming to a close, some of the devastating effects of Covid-19 are beginning to recede. Relief comes as lockdowns end in some countries, and hospitalization rates lower in others. Fewer cases, coupled with all the perks that come with lockdown-free societies, are great news. However, one glaring inefficiency continues to pose a significant challenge to all world markets: the supply-chain crisis.
Over the past year, delayed ETAs and ETDs resulting from shipping container overflows at ports have challenged every link in the supply chain. Moreover, fewer longshore workers due to an influx of covid-19 delta variant cases, have exacerbated the supply chain crisis.
The State of Shipping: In Review
In last August's blog, Island Leaf delved into the effects Covid-19 has had on the global supply chain and shared some of the logistical challenges we've encountered. First, we noted the initial trauma Covid-19 wrought on people's wellbeing and the world economy. Then, we wrote about the difficulties that exporters like Island Leaf faced, including longer-than-average transshipment times for goods passing through Indian ports and the absence of space on many container ships worldwide. Island Leaf experienced these difficulties for shipments originating in Australia and Europe with LATAM, SE Asian, and the United States as destinations.
To demonstrate the level of risk Covid-19 dished out to the commodities trade, we explained why the vast majority of commodities buyers and sellers expressed a reluctance to nominate themselves as shippers of goods. This reluctance resulted in both parties wanting to either buy or sell on an FOB incoterm only.
We also shared the irritating experience of having goods further delayed due to the seven-day-long Evergiven conundrum in the Suez Canal. The blockage caused by the Evergiven resulted in the rerouting of some material we sold, extending transit time and headache pain by 35 days.

In the second part of the blog we examined how the shipping crisis-affected world markets. Citing astronomical price increases for shipping 20' and 40' containers from Asia to Europe or North America, we explained that many smaller exporters were making razor-thin margins or operating at a loss.
Finally, we made a few concluding remarks, based on both our experience and the most current news at the time. We attempted to offer some "guidance" and predicted the state of shipping in the coming months. Ultimately, we did not think there was any reason to believe the supply chain crisis would resolve itself, or be resolved, by the end of the first quarter in 2022. We based this claim on two facts. First, neither government, port, nor private company efforts were relieving any supply-chain bottlenecks. Second, the highly virulent delta strain had just begun ripping through the United States and other countries, pausing hiring, and causing breakthrough cases.
Three months later, in the waning days of 2021, what exactly is the prognosis for this supply-chain crunch? This month, we'll go straight to the one of the main points of the supply chain crisis: various ports around the world. We'll examine their situations, along with the repercussions felt by businesses. Then, we'll look at some of the possible solutions that port authorities and governments should pursue. Finally, we'll touch on how the Covid-19 Supply Chain Crisis is already changing how many US-based businesses operate. This change in operations may indeed set a new precedent for the future, and change the way world markets rely on global supply chains. Will the change in operations contribute to supply-chain solutions?
Part 1: Sluggish Container Processing Effect on World Markets and Supply Chains
In our last shipping blog, we mentioned that many ports faced severe congestion issues. For example, in August, the US-based ports of Long Beach/Los Angeles faced significant ship backlogs, with over 30 anchored just off the coast of California. In addition, a dearth of workers and ground transport, combined with a large number of incoming goods due to a swift recovery of the US economy, resulted in a slower than average turnover time of containers and contributed to a 13-year high average inflation rate of 5.4%. Thus, the number of port workers was insufficient to unload the number of containers waiting, creating the present supply-chain-crippling backlog.

In late August of 2021, when we published our first shipping blog, the number of container ships and bulk vessels unable to enter port registered in the high 30s. As we write this blog in the first week of November, that number has tripled, with over 100 ships anchored off the shores. To give readers an idea of how devastating this is to the US economy, Long Beach/LA ports process over 40% of total US imports.
A similar scenario continues to play out in other ports around the world too. Recent Covid outbreaks and subsequent lockdown or quarantine measures have resulted in very sluggish container-processing times. For example, as of November 1st, Singapore, a major transshipment port, had over 50 vessels anchored off its shores, awaiting berthing.
Some Chinese ports are also facing bottlenecks. For example, the port of Ningbo/Zhoushan and the Port of Shanghai, just to the north of Ningbo, have a combined total of over 70 vessels anchored off their shores. Many of these vessels hold empty containers or no containers, awaiting the loading of Mainland-Chinese manufactured finished and semi-finished goods.
Elsewhere in Asia, Port Klang (Malaysia), the port of Bangkok, Port Jebel Ali, Port Qingdao, the port of Busan, and Port Tanjung Priok (Indonesia) are all facing port congestion rates of over 10%. This congestion means these ports have a backlog of ships awaiting berthing, resulting in slower turnaround times and delays.
One of the main drivers behind anchored ships at port outskirts is a lack of workers to offload containers. When ports have only a sub-optimal number of human resources available, offloading and onloading is compromised. Additionally, countrywide lockdowns also slow the transport of goods from port of arrival to final destination, further snarling an already hamstrung supply chain.
Very Few Hands at Port Means Higher Costs
Australian ports also felt the pain of the supply chain crisis, as the delta strain severely bloodied the nose of Australian exporters. Reacting to a surge in delta-variant cases, Western Australia, New South Wales, Victoria, and South Australia implemented notorious lockdowns in mid summer. Not only did the lockdowns and acceleration of cases deal a blow to many Australians' daily lives, they also critically challenged Australian exports. Island Leaf was amongst those affected.

Some results of this conundrum included three-to-four-week departure-date delays, processing sites being shut down for a matter of weeks, thus disallowing the continuation of some material, and changing shipping routes to LATAM from an eastwardly direction (IE Melbourne-New Zealand-LATAM) to a Westerly one (Melbourne-Mersin-Valencia-LATAM). Unfortunately the lockdowns mutated 40-day average transit times to painfully sluggish 75 day transit times.
Another casualty of the supply chain crisis has been purchasers' bank accounts. Indeed, the average price for one 40' HC standard shipping container from Asia to North America has increased to over $10,000. Thus, for example, Island Leaf has seen furious upward price velocity over the past 12 months for freight—rates from Australia to LATAM have gone from around $2,200 per 40' container to just about $9,600; rates from Australia to Charleston have also increased by a few thousand dollars as well.
We've talked to several parties like suppliers, buyers, and freight forwarders about the current state of freight costs. Here's the universal conclusion: shipping companies are enthusiastically reeling in record profits, leveraging a meager supply of containers related to consumers' insatiable demand for goods on the world market.
While many shipping line executives bask in success defined by record profits, a multitude of others, including producers, traders, port workers, and customers, stew with frustration. How much longer will consumers have to put up with these insanely overpriced shipping rates? When will these annoying and business-constricting vessel departure/arrival delays end? And when will port congestion, apparent in places all over the world, finally begin to clear up? Ultimately: when is this damn shipping crisis going to conclude?
The short and disturbingly unfortunate answer is, according to many experts, sometime in 2023. For many parties (excluding shipping lines), enduring this crisis for at least another 14 months is impossible. This fact begs the question: what are the possible solutions for this mess?
Part 2: An Attempt to Cope: A Silver Lining for World Markets?
Several companies and governments have already set plans into motion that aim to fix this crisis. Some companies are pursuing quick-fix remedies, like Maersk acquiring an air-cargo company and giant retailers like Costco and Walmart chartering their own vessels. However, it's challenging to determine what kind of effect, if any, these actions will have on prolonged port processing times and the backlog of anchored ships.
Actions taken by governments may help mend supply chain problems. While the United States has finally passed an Infrastructure bill, the construction that will update port capacity and improve container processing time does not begin until 2022. Moreover, it will take time to complete the updates. The quickest part of the bill to be implemented is the doling out of federal funds to ports to hire more workers or lease adjacent storage space, which will take a few months to hit port bank accounts.
The bad news is, the world economy needs immediate action. Given that the supply-chain crisis's initial pain point emanates from bottlenecks, the first place to begin the fixing is at a country's point of entry: ports.

California's Other Big Port
After watching various news reports on TV and social media, and reading about supply-chain updates, one might believe that the supply chain crisis has crippled every single port on the planet. Fortunately, the market-research team at Island Leaf delved into some statistics and under-the-radar port news. As a result, we've concluded that the impending-doom zeitgeist may have a silver lining. While the ports mentioned above exhibit reasons for concern, there are a few under-reported reasons for mild optimism.
The other major port in California, the Port of Oakland, recently exclaimed that they lacked a ship backlog. What's more, Oakland has experienced a decline in imports since September 2021. The port director, Bryan Brandes, proclaims that the port is "…open for business" and therefore implores backlogged vessels, or vessels heading to a port with severe backlogs, to call there. Can a relative abundance of space at Oakland relieve some of the pressure from Long Beach/LA?
Although the Port of Oakland can handle about 25% of Long Beach/Los Angeles' capacity, it can berth same-sized container ships with a 50-foot port depth. According to a recent report, a Bay Area journalist notes that Port of Oakland authorities anticipate picking up some of the Long Beach/LA backlogs, especially with the beginning of the holiday season. The Port of Oakland seems to be up to the task, as they've recently hired several longshore workers and finished installing new offloading equipment.
Unfortunately, one port partially bailing out another will not solve the global problem of container backlogs. But, faster container processing time at importing countries (like the United States) makes shorter container turnaround times possible. So, theoretically, more empty containers will find their way back to major exporting countries. We also need to take a closer look at the export data from major exporting ports—as fewer ships leaving means fewer backlogs at the destination.
We can get a rough idea of a country's export volume by looking at its trade surplus. For example, although China, the world's largest exporter, had about a 5% fall in its trade surplus with the United States from September to October 2021, its worldwide trade surplus was up about 27% for the same period. These data mean that while US demand momentum is losing some velocity, worldwide demand for Chinese goods, many of them packed in shipping containers, remains strong. Additionally, the export-heavy economies of South Korea and Taiwan also saw their export surpluses grow in the same period. But, as we mentioned above, many of these ports located in net-exporting countries are now dealing with ship backlogs of their own.
What does this all infer? While the Port of Oakland is willing to both hire more longshore workers and offer itself as an alternative destination, the fact remains that there are several offloaded containers already at port that are taking up space. Unfortunately, the number of chassis, steel trailers upon which shipping containers are transported, is too low to accommodate the current container overflow. While the situation appears dire, signs of solutions are beginning to emerge.
Part 3: Possible Solutions and Great Implications

Rerouting
An ideal move would be for some of the ships anchored at Long Beach/LA Ports to reroute to Oakland. Logistics professionals would need to organize arriving cargo onwards, but rerouting should save time given the relative proximity to Southern California. While the rerouting of backlogged ships from Long Beach/LA to the Port of Oakland would not completely reverse the problem due to its smaller capacity, it would offer some relief.
On the east coast, the major ports of Savannah and New York are also experiencing backlogs, but the nearby Port of Charleston (which recently installed new unloading machinery) is not. As with the Port of Oakland situation, logistics managers should consider rerouting some east coast-backlogged ships to Charleston.
Space and Acquisitions: A New Trend for World Markets?
The supply chain problem does not end when a newly increased number of cranes hoist tardy containers off of delayed vessels: the scarcity of container storage space at destination ports is the next challenge in the global supply chain. However, Ryan Peterson, CEO of Flexport, a freight forwarder, recently offered some insights via tweet. He emphasized that increasing the shipping container legal stack height from two to four would drastically alleviate offloaded containers.
Luckily, the mayor of Long Beach, Robert Garcia, heeded the call and, in late October, issued an emergency order to increase the legal stack height from 2 to 4 containers. Not only should this alleviate some spacing issues, but it should also free up a few thousand chassis for delivery. However, this solution has a trade-off: higher container stacks might make it more challenging to locate containers, further delaying their delivery to the final destination.
To quell ETA delays, some companies are accelerating their hiring processes. UPS, a leading ground delivery and logistics company, is a prime example. UPS, keenly aware that it must get "butts in seats" as soon as possible with the holiday season approaching, has streamlined its hiring process. Candidates apply online and hear back, within 30 minutes, if they've received the job or not. UPS has noted that over 70% of all hires are done via a smartphone APP. UPS aims to hire over 100,000 workers in the next few weeks.
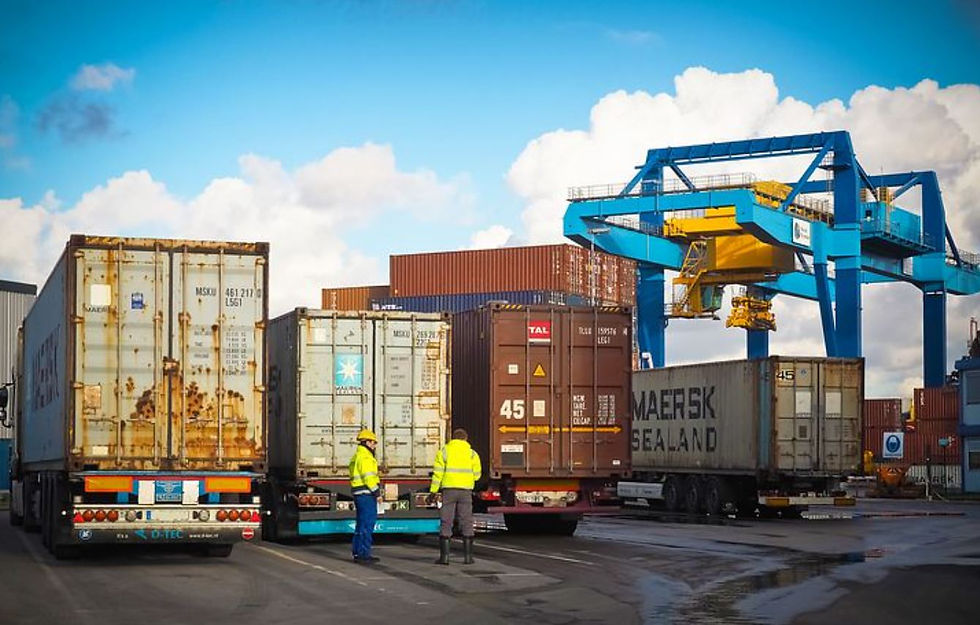
Another development in the United States that will undoubtedly affect the future of the supply chain and the supply chain's effect on world markets is a growing number of companies' decision to bring production back to American shores. This is partly because the shipping crisis has exposed the complex global supply chain's endemic frailties. Although capital expenditure and wage increases may cost companies more in the short term, greater control over supply chains and fewer transshipment points will hedge risk, saving money over the long term.
To further control supply chains, some large firms are resorting to an acquisition strategy. For instance, Sherwin-Williams, a paint manufacturer, recently acquired Specialty Polymers, an Oregon-based resin producer. Specialty's resin is a crucial ingredient in paint.
A different example of this strategy will affect the recycling industry. Recently, American packaging firm ProAmpac acquired two British recycling companies. Ultimately, ProAmpac's primary goal is to secure sustainable plastic closer to its European-based manufacturing operations so that it does not have to rely on importing material from other countries.
Both Sherwin-Williams and ProAmpac's decision to acquire companies crucial to their supply chain highlights examples of companies wishing to exhibit more control of raw materials while (theoretically) relying less on global shipping.
Part 4: Concluding Questions
Despite initial action taken by logistics, government, and port officials, the supply chain woes at several world ports remain, and they will probably linger into 2022. But, changes in certain regulations that apply to container space and stacking, as well as other ports posing alternative call destinations demonstrate that actors are already beginning to implement long-term solutions. And, major retailers are willing to take matters into their own hands by chartering their own vessels. However, a lack of trucks, chassis, and rail capacity remains. This is a problem logistics professionals must solve in order to begin relief.
One of the most interesting points is the fact that many US manufacturers are bringing production closer to home to reduce supply chain risk. Will production re-shoring and an effort to bring raw-material sourcing closer to processing sites actually hedge risk? And if so, what does this mean for global supply chains, world market efficiency, and the shipping industry as a whole? Will there be less demand for ocean shipping in the years to come?
Island Leaf Commodities, a trading firm familiar with commodities and world markets, works with a team of exporters, freight forwarders, and others involved in the logistics industry. Ultimately, the people with whom we work are those who we’ve spent years developing relationships with.
Visit our website at www.islandleaf.co for more information about products and our business philosophy.
Comments